Construction
Manufacturers in the construction industry have come to expect the best performing robotic solutions available globally.
Mexx Engineering® is one of the few robotics and automation companies in Australia. We are known for designing and manufacturing complete lines that are built to handle a range of functions from upstream processing, sorting and packing through to the end of line palletisation.
Mexx Engineering® can streamline the construction industry using innovative and versatile systems such as:
Our top-of-the-line robotic systems can accelerate and streamline all these processes through:
The implementation of robotic automation within the construction industry offers incredible potential for improved safety, quality and productivity by enhancing process monitoring and control.
With a high number of fully automated robotic systems, construction parts and materials will become much more consistent, and with more top quality. By removing human error and unpredictability out of the equation, a fully automated machine is advantageous, especially in improving speed, efficiency and repeatability. By doing so, we also cut down waste from human mistakes and ensure overall quality.
Automated Concrete Test Lab
The Automated Concrete Test Lab serves as a storage and lab testing facility that consists of 3 main processing areas; the Incoming Cores, the Limewater Storage and Handling, and the Core Testing.
KEY FEATURES OF THE AUTOMATED CONCRETE TEST LAB:
- 2 ABB Robots for core handling
- Dedicated de-mould and clean station/machine
- In-feed conveyor system for moulded cores
- Out-feed conveyor system for returning demoulded moulds
- Control the interaction of the various system components.
- HMI interface communicates data of each core at all stages of transport and testing
- Automation of grinding machine and location of the water tank
- Automation of Compression Testing Machine
- System safety interlocked and guarded as per Australian and New Zealand Standards
Automated Concrete Test Lab
Automated Concrete Test Lab (Slideshow)
Robotic Weld Cell
The Robotic Weld Cell performs robotic welding on a fixed table (FX) or in a rotating unit (RD). The rotary unit reorients the product during the welding process. The system ensures the operator is protected from weld arc. The system operates automatically ensuring maximum production output. The robot is always welding while you unload finished products and load new parts.
KEY FEATURES OF MEXX WELD CELL:
- Rotary axis coordinated with a welding robot
- Various Fronius power source options to suit customer's requirement
- TCS with Bulls-eye - for torch service & calibration
- Notification light tower and alarm to notify the operator of the cell status and material outages.
- Operator interface through Robot Teach Pendant.
- System contains fixed part loading locations for each of the parts to be welded
- System safety interlocked and guarded as per Australian and New Zealand Standards
Robotic Weld Cell (Video)
MexxWeld RD-RD-K 2600 (Slideshow)
MexxWeld RD-RD-K 1520 (Slideshow)
MexxWeld FX-RD (Slideshow)
Robotic Paint Booth
The Robotic Paint Booth is a complete painting facility. The robotic system can monitor and control the paint consistency and spray area. A fully automated product handling system manages the product through all painting, handling, and baking process.
KEY FEATURES OF A ROBOTIC PAINT BOOTH SYSTEM
- ABB Robot
- Integrated bake oven
- Custom spray booth with dry medium air filtration
- Temperature controlled paint booth to maintain consistent paint environment all year round
- The integrated automatic indexing system
- Notification light tower and alarm to notify the operator of the cell status and material outages.
- Operator interface through HMI
- System safety interlocked and guarded as per Australian and New Zealand Standards
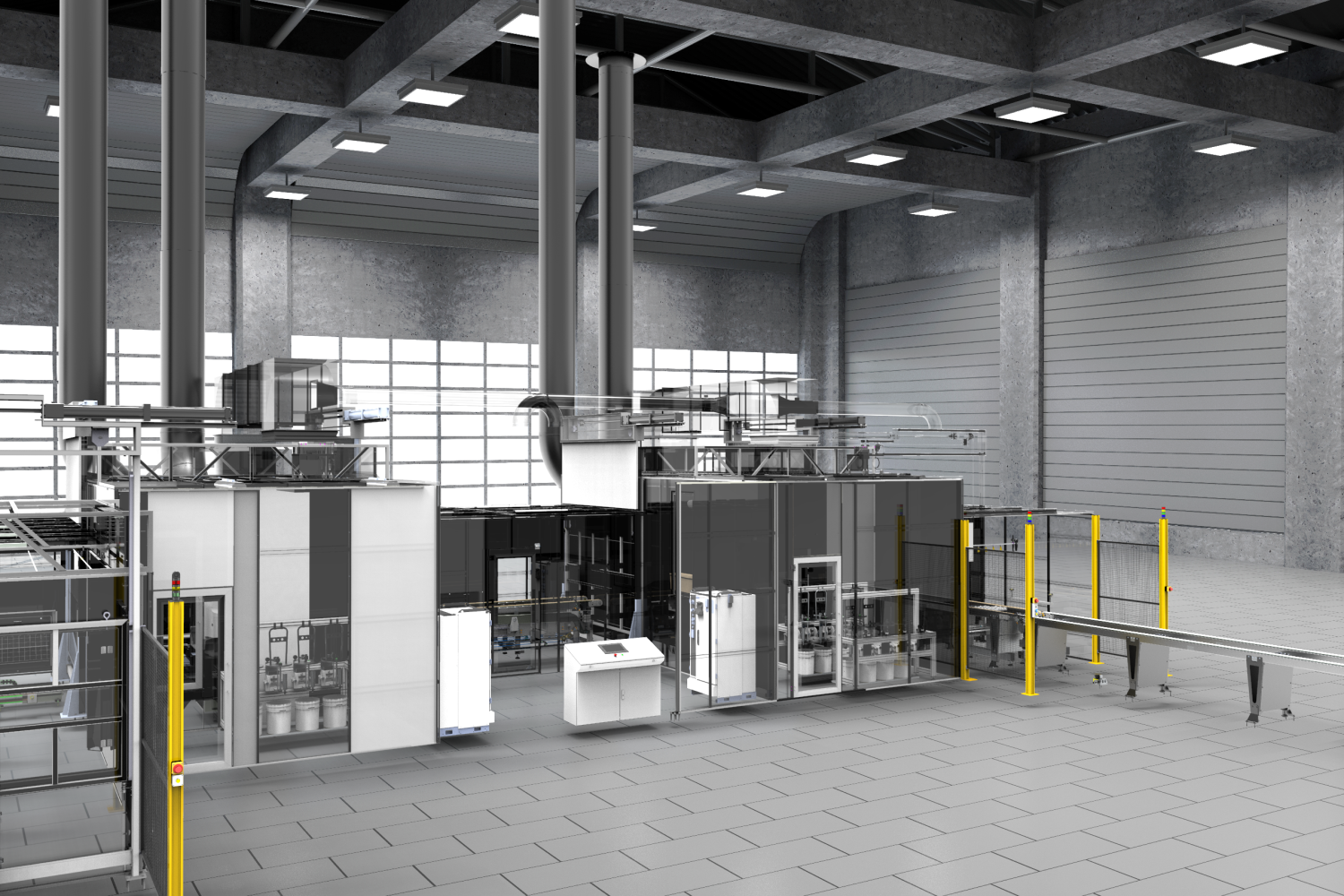
Robotic Paint Booth
Robotic Paint Booth (Slideshow)
Robotic Paint Booth (Video)
Vision System
The Vision System checks the orientation and quality of a product. It inspects the product for damage and determines how to handle it. A dedicated feeding system that automatically spaces the product can be added as an option.
KEY FEATURES OF THE VISION SYSTEM:
- 5” touch screen for operation and production information
- 20” Display and roller trackball for camera system control and setup
- Light tower for status indication
- PLC Controlled - Independent floor mounted frame for stability
- Central control via HMI
- System safety interlocked and guarded as per Australian and New Zealand Standards
Vision System (Video)
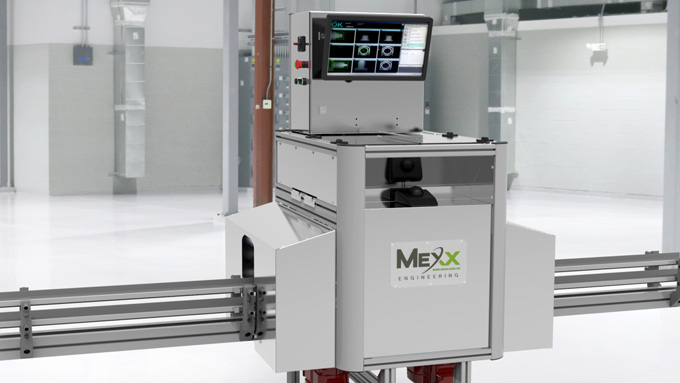
Vision System (Aluminium)
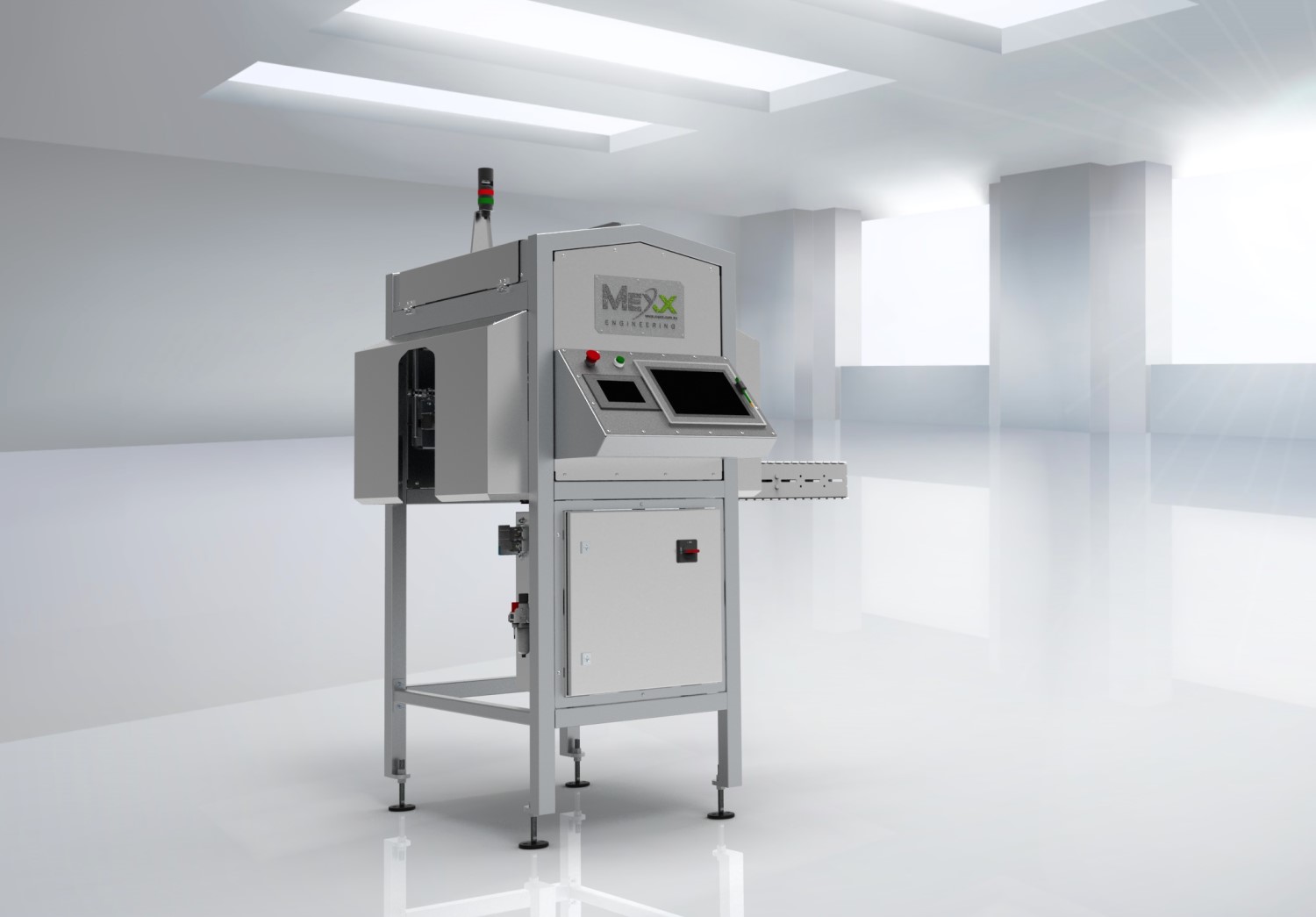
Vision System (Stainless Steel)