Pharmaceuticals & Neuroceuticals
Manufacturers in the pharmaceuticals & neuroceuticals industry have come to expect the best performing robotic solutions available globally.
Mexx Engineering is one of the few robotics and automation companies in Australia. We are known for designing and manufacturing complete lines that are built to handle a range of functions from upstream processing, sorting and packing through to the end of line palletisation.
Mexx Engineering can streamline the pharmaceuticals & neuroceuticals industry using innovative and versatile systems such as:
- Autobagger System
- Bi-directional Palletiser and Depalletiser System
- Bottle Palletiser System
- Debagger System
- Conveyor System
- Continuous Bottle Turner
- Vision System
The implementation of robotic automation within the pharmaceuticals & neuroceauticals industry offers incredible potential for improved safety, quality and productivity by enhancing process monitoring and control.
The pharmaceutical industry relies on automated robotic systems for increased efficiency in both manufacturing and packaging processes. Automated systems provide the flexibility required by the industry-leading to lower costs and consistent product quality.
The modular stainless steel components (for hygienic conveyors) combine to create the same innovative solutions as the more common (aluminium) systems, including accumulation and elevation systems.
Medical technology needs a distinct degree of proficiency and precision in the production of parts intended for this industry. At the same time, the industry faces soaring demands due to the rivalry from the world-wide market and increasing customer expectations. To sustain demand, it is fundamental to keep manufacturing high-quality products with flexibility and within a brief distribution window.
Pharmacy automation also further eliminates the chances of human error and streamlines your workflow by using a machine to assist in counting, packaging, capping, dispensing systems, storage and retrieval systems and labelling prescriptions.
The use of robots in the pharmaceutical industry has many advantages and benefits when it comes to speed. Robots can achieve tasks around four times faster than individuals can and additionally can be worked 24 hours a day.
Autobagger System
The Autobagger System will reliably collate and bag products for transport. This system can be manufactured either as a stand-alone OEM product or fully-automated turnkey system as part of a larger production line.
KEY FEATURES OF THE AUTOBAGGER SYSTEM:
- Automatic bottle collating and bagging machine
- Uses continuous bags that can be custom made to length for each product
- Versatile conveyor in-feed options available
- Dual in-feed of 2 products simultaneously
- The system accommodates both half size and full-size bags simultaneously
- Servo controlled for maximum flexibility
- Automatic pallet in-feed system
- Integrated pallet de-stacker (optional)
- AGV load positions for pallets or layer boards
- System safety interlocked and guarded as per Australian and New Zealand Standards
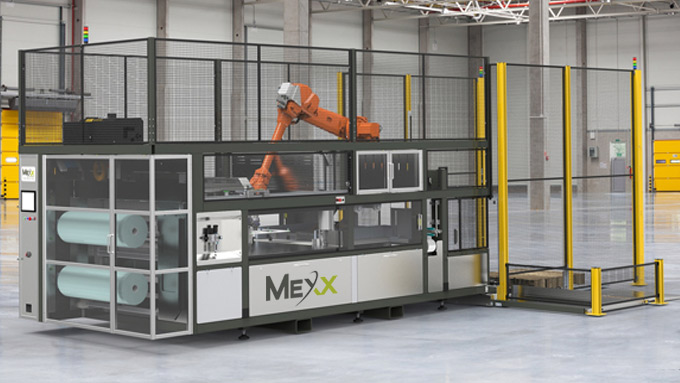
Autobagger System MK3
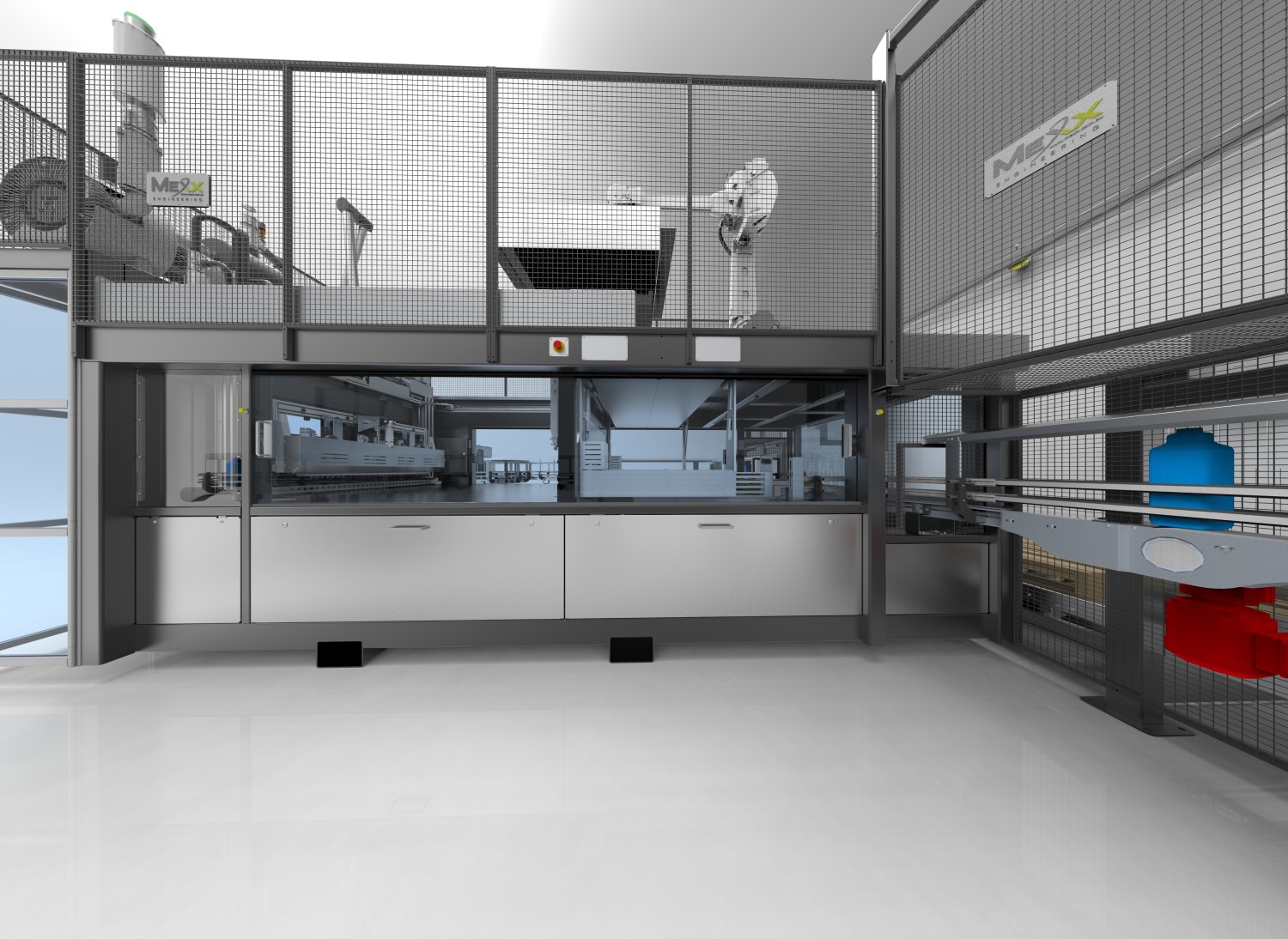
Autobagger System MK5
Autobagger System (Video)
Bi-directional Palletiser and Depalletiser System
The Bi-directional Palletiser and Depalletiser System is designed with our universal bottle vacuum head to handle various bottles sizes. This versatility in combination with our pallet in-feed and out-feed system gives customers a versatile solution to suit many bottle lines.
KEY FEATURES OF THE BI-DIRECTIONAL PALLETISING AND DE-PALLETISING CUBE:
- Multifunctional bottle palletising and de-palletising system can perform various tasks on-demand as follows:
- De-palletise from pallet to conveyor
- Palletise from conveyor to pallet
- Use as a buffering system for inline blow moulding as the system will feed bottle as well as palletise bottles, as required
- Central control via HMI
- One ABB robot equipped with a Mexx Universal Bottle Vacuum Head
- Automatic multi-pallet in-feed and out-feed
- System safety interlocked and guarded as per Australian and New Zealand Standards
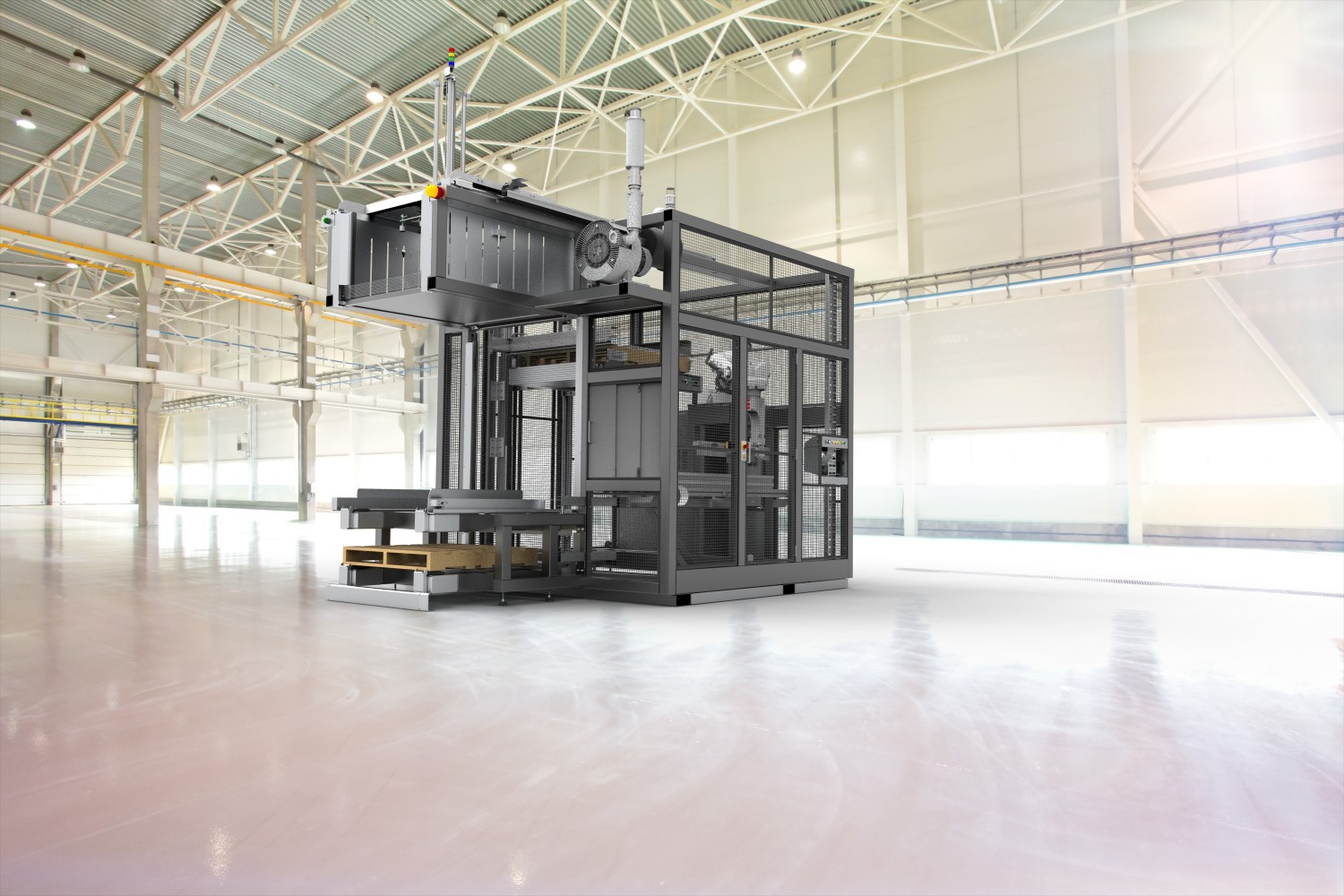
Bi-directional Palletising and Depalletising Cube
Bi-directional Palletising and Depalletising Cube (Video)
Bottle Palletiser System
The Bottle Palletiser System will pick and place bottles onto layers on a pallet. The system can have one robot picking up from 2 different conveyors and dropping off bottles onto two separate pallets.
KEY FEATURES OF THE BOTTLE PALLETISER SYSTEM:
- Seamless bottle palletising system
- Central control via HMI
- One ABB robot equip with a Mexx Universal Bottle Vacuum Head
- Automatic multi-pallet out-feed
- System safety interlocked and guarded as per Australian and New Zealand Standards
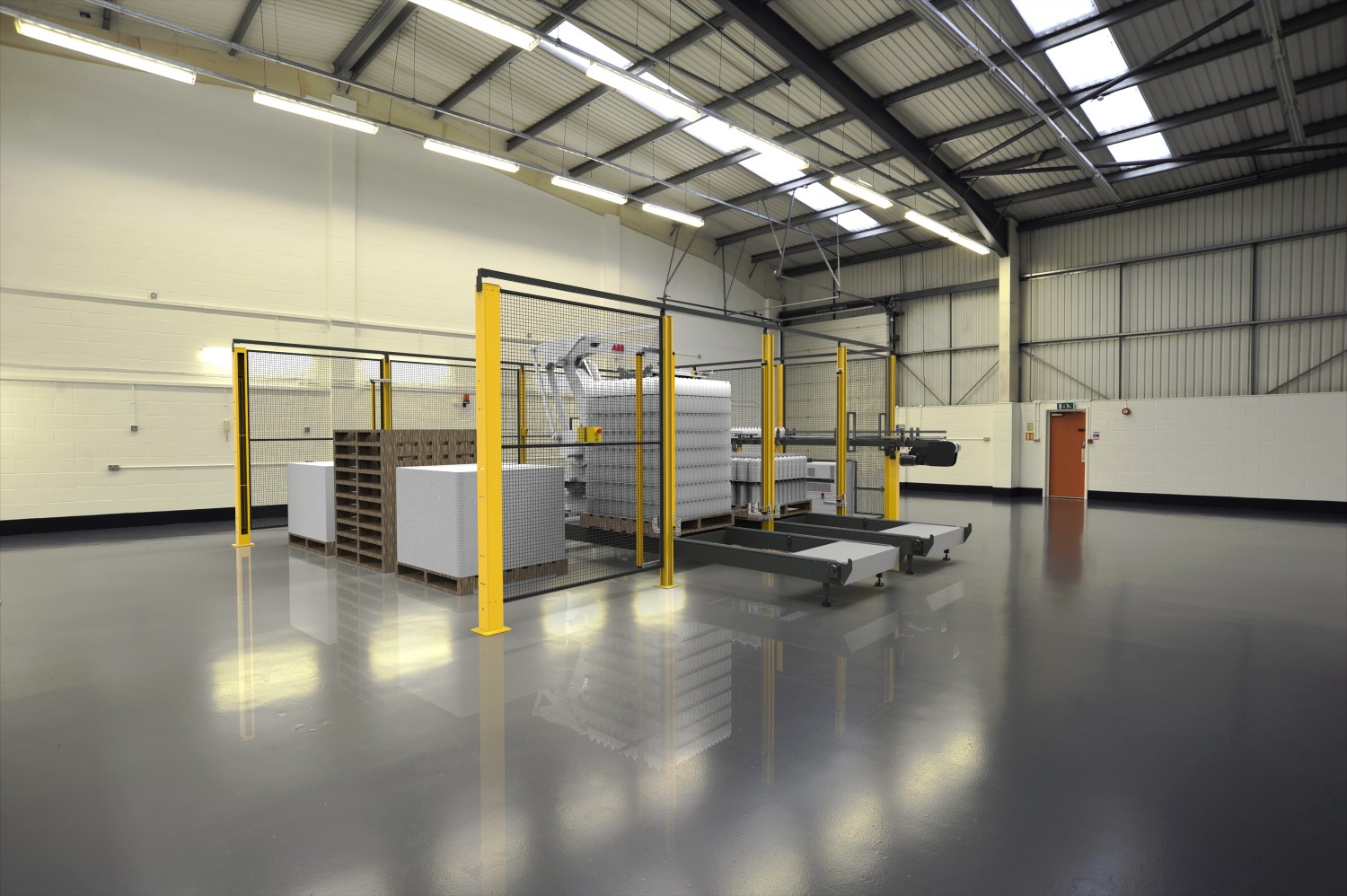
Bottle Palletiser System
Bottle Palletiser System (Slideshow)
Debagger System
The Debagger System will reliably unseal bagged products, pick and place them into a conveyor in preparation for further processing. This system can be manufactured either as a stand-alone OEM product or fully-automated turnkey system as part of a larger production line.
KEY FEATURES OF THE DEBAGGER SYSTEM:
- Bottles are automatically removed from the bag
- The system will accommodate full size & half size bag
- Automatic bag de-palletising
- Semi-Automatic version also available
- Bags are cut with precision without damaging any bottles
- Automatic bag collection and compression into a waste sock
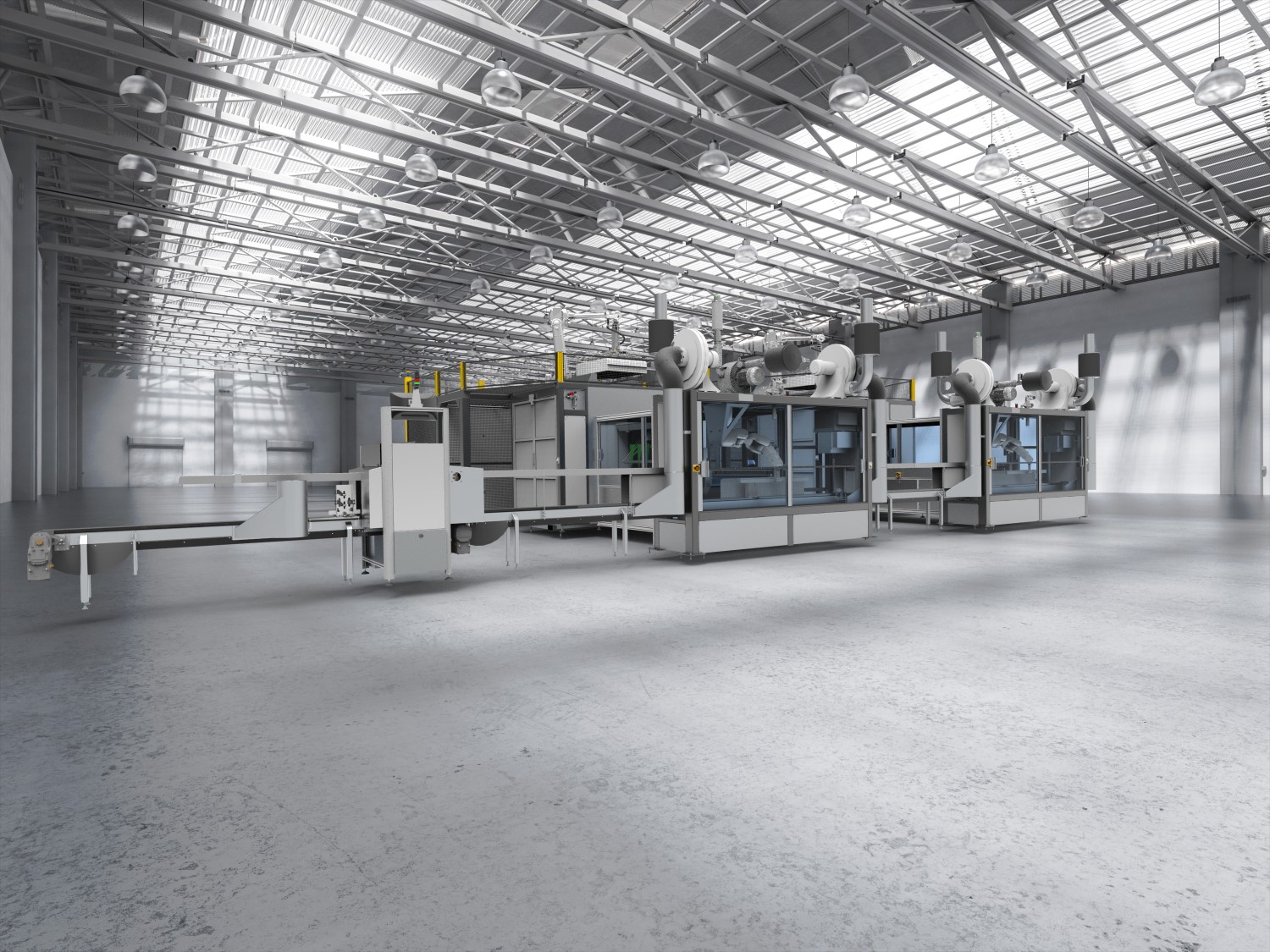
Debagger System
Conveyor System
The Conveyor System controls product delivery from point A to point B with the use of various conveyor chain materials. Its guide rail system is fully adjustable to ensure continuous movement of the bottle around a curve.
KEY FEATURES OF THE CONVEYOR SYSTEM:
- Aluminium or Stainless conveyor system
- Includes automatic self-centring guide rail adjusters
- Integrated transfers from upstream conveyors
- Integrated transfers to downstream conveyors
- High-speed with virtually no back-pressure and bottle gaps
- Accumulation system
- Full system control
- System safety interlocked and guarded as per Australian and New Zealand Standards
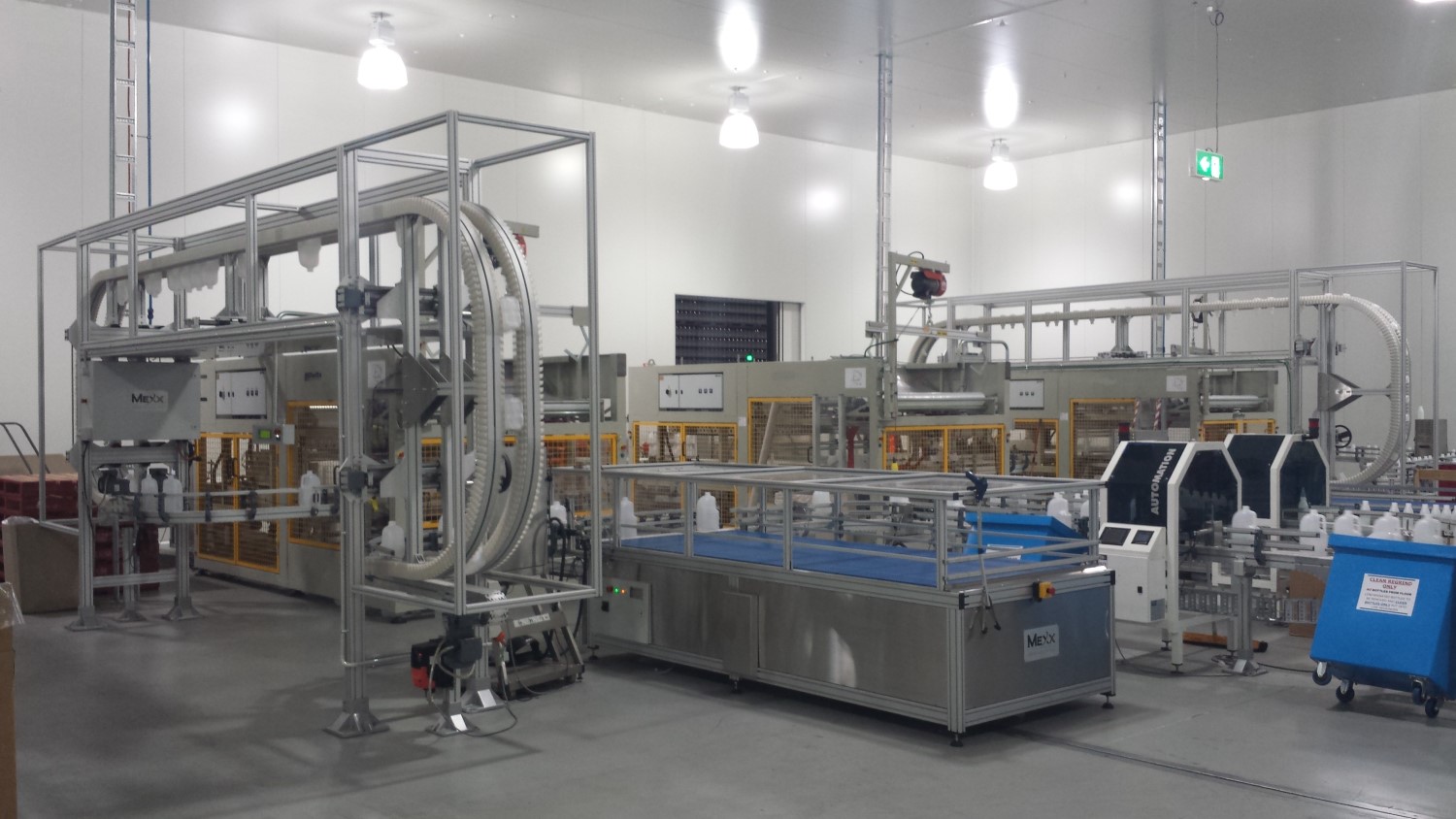
Conveyor System
Conveyor System (Slideshow)
Conveyor System (Video)
Continuous Bottle Turner
The continuous bottle turner is designed to reorient bottles on a conveyor line. The bottles are turned by independently adjusting the speeds of the two belts with respect to the conveyor speed. The system can either be mounted on the floor or in the ceiling as an overhead version.
KEY FEATURES OF THE CONTINUOUS BOTTLE TURNER:
- Two mounting options available (floor standing or roof hanging)
- The roof hanging kit includes a wired remote control pendant
- The remote control is available separately for floor standing models
- Both mounting options connect to the same base device, so changing the mounting method in the future is as easy as purchasing the appropriate mounting kit
- System safety interlocked and guarded as per Australian and New Zealand Standards
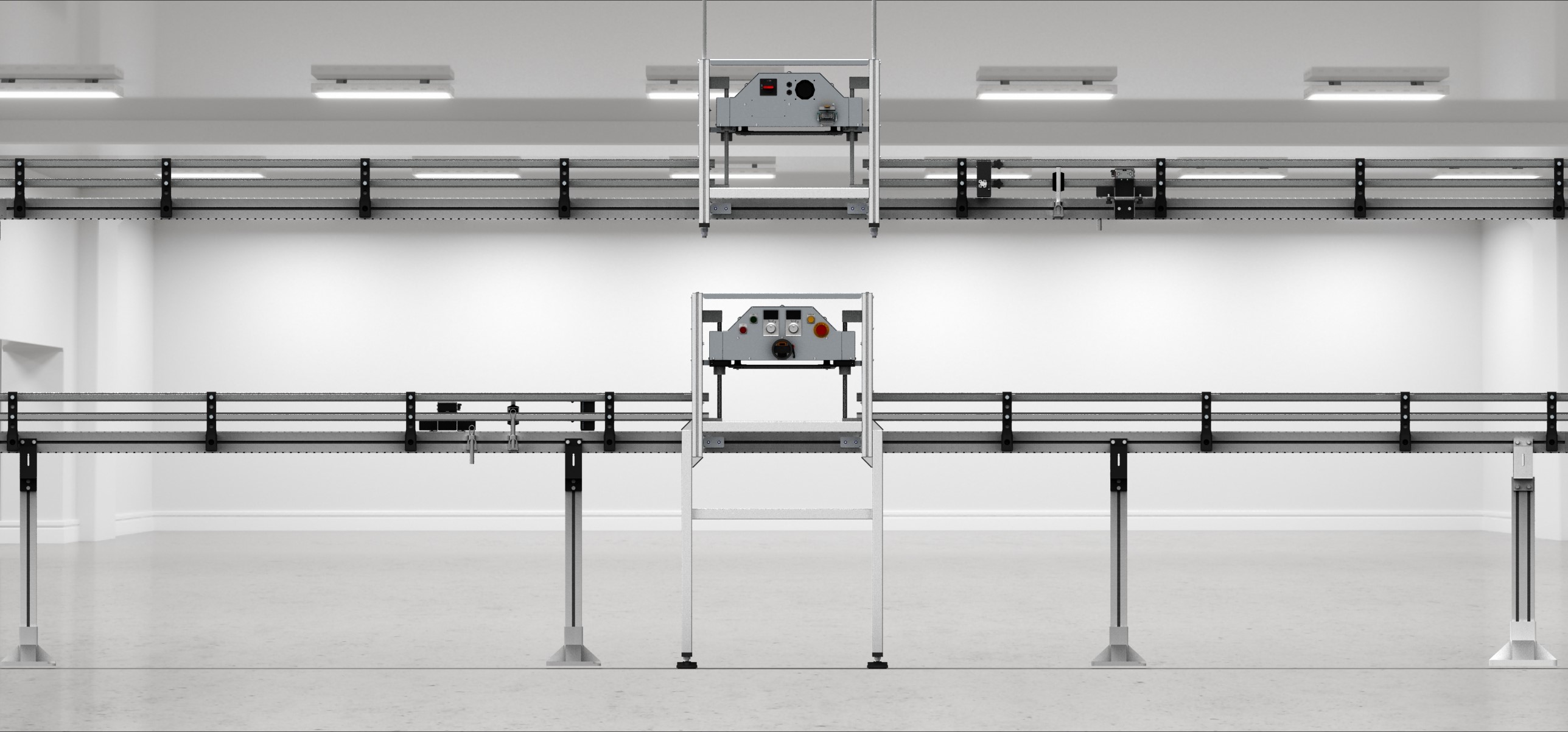
Continuous Bottle Turner (Ceiling Mounted and Floor Mounted)
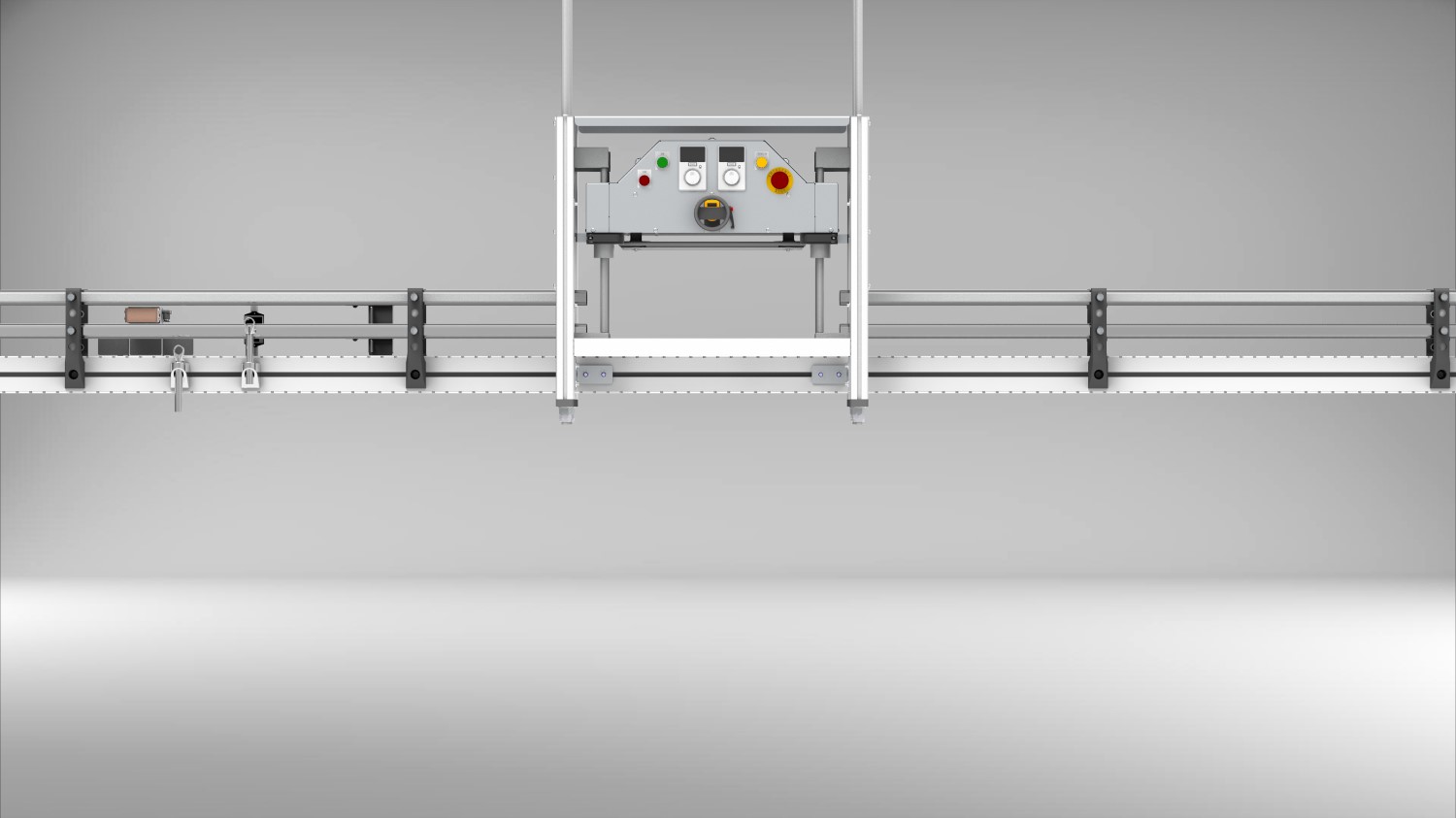
Continuous Bottle Turner (Ceiling Mounted)
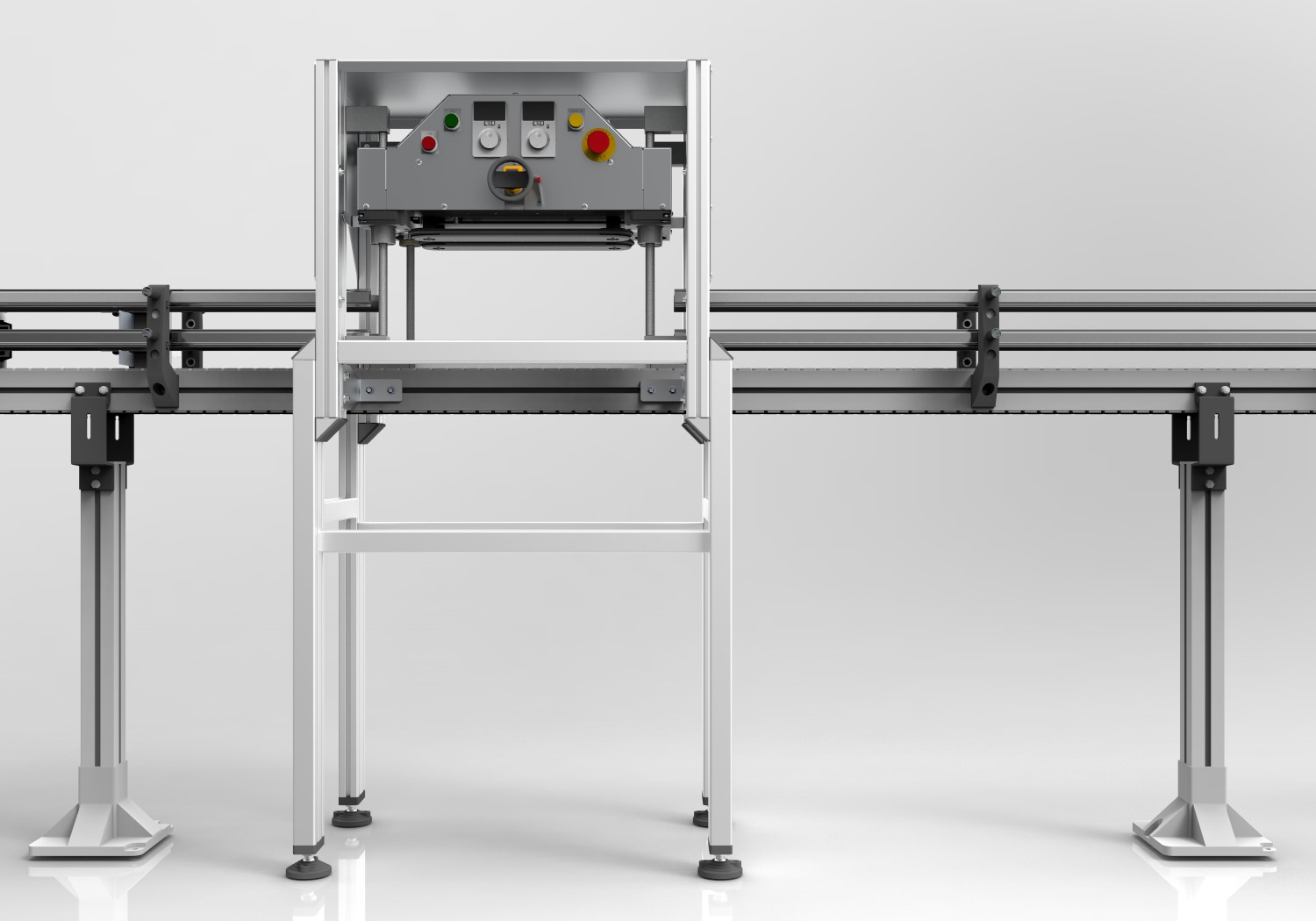
Continuous Bottle Turner (Floor Mounted)
Vision System
The Vision System checks the orientation and quality of a product. It inspects the product for damage and determines how to handle it. A dedicated feeding system that automatically spaces the bottles can be added as an option.
KEY FEATURES OF THE VISION SYSTEM:
- 5” touch screen for operation and production information
- 20” Display and roller trackball for camera system control and setup
- Light tower for status indication
- Eject bottles using air blast
- PLC Controlled - Independent floor mounted frame for stability
- Central control via HMI
- System safety interlocked and guarded as per Australian and New Zealand Standards
Vision System (Video)
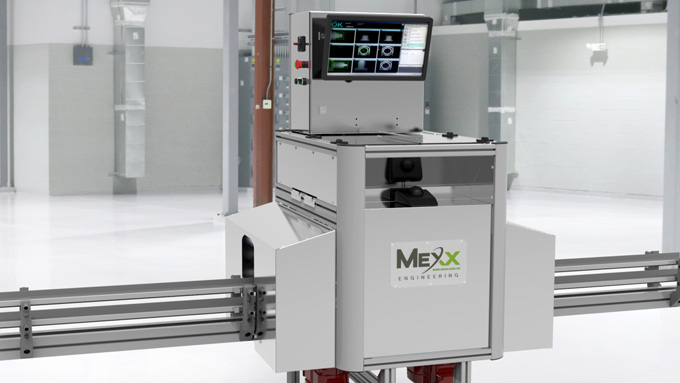
Vision System - Aluminium
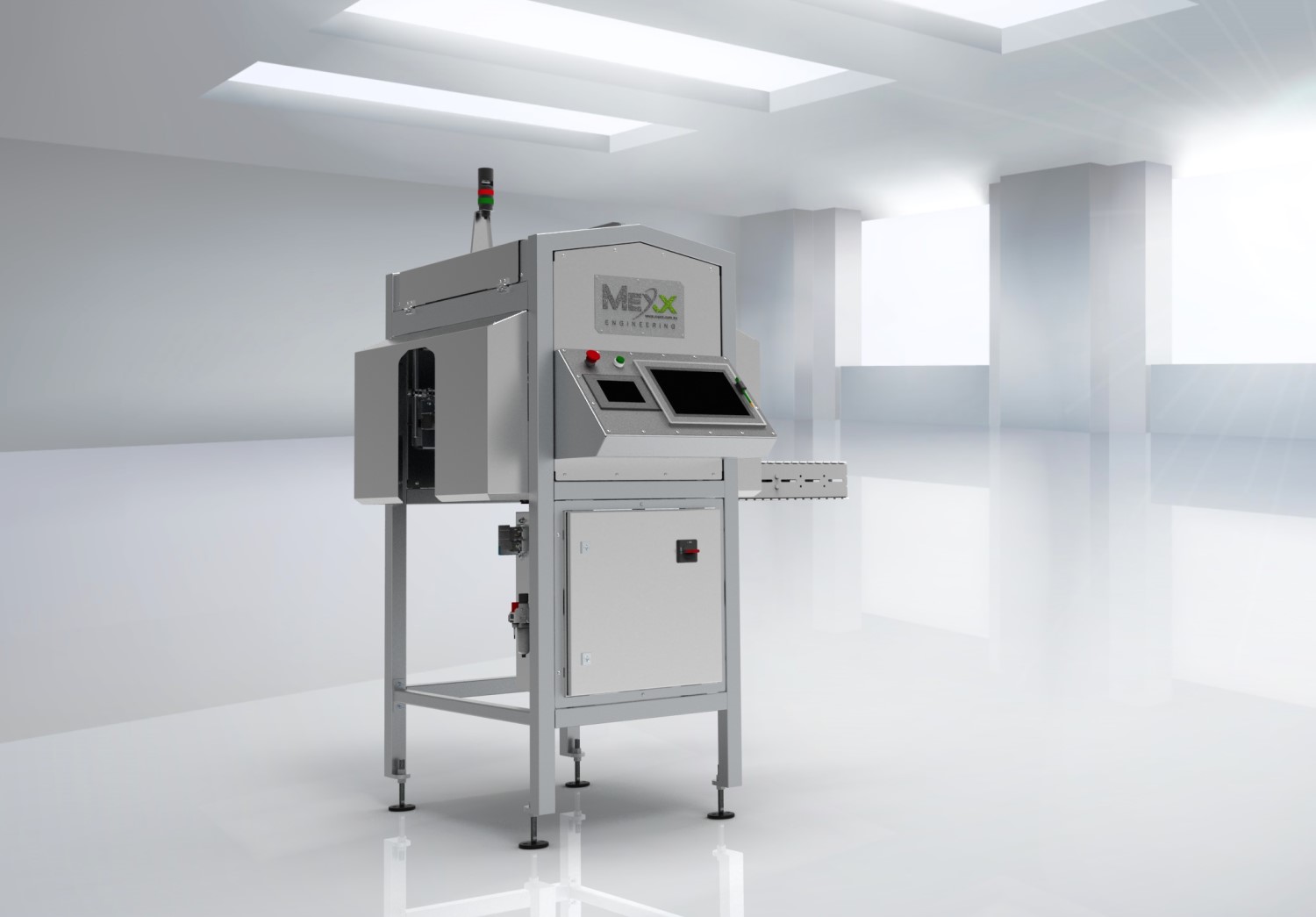
Vision System - Stainless Steel
Custom Design & Automation
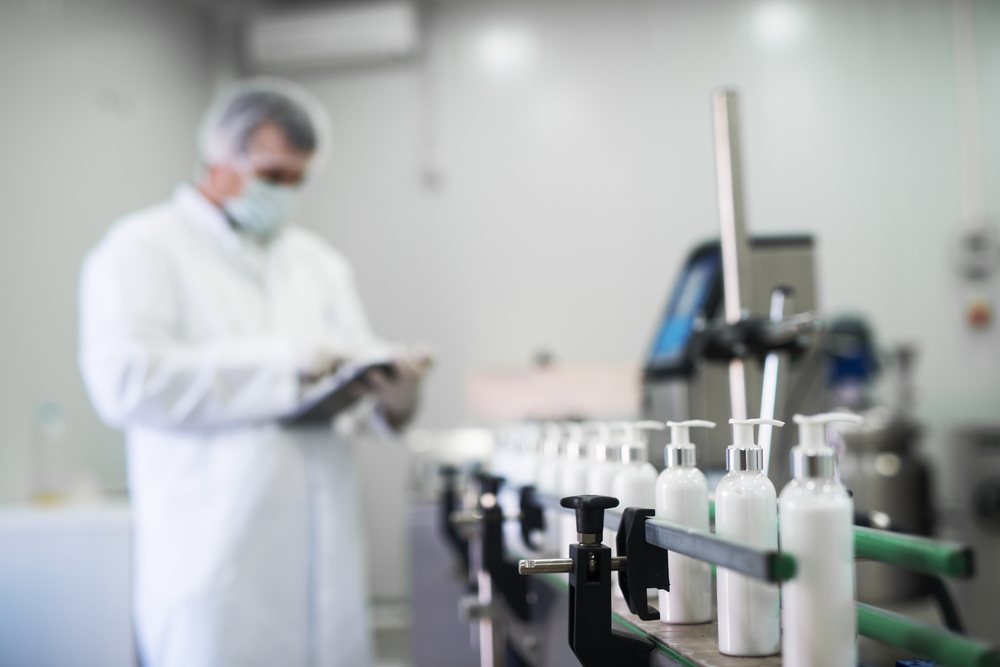
Conveyor Machine for lotion bottles (Concept Image)
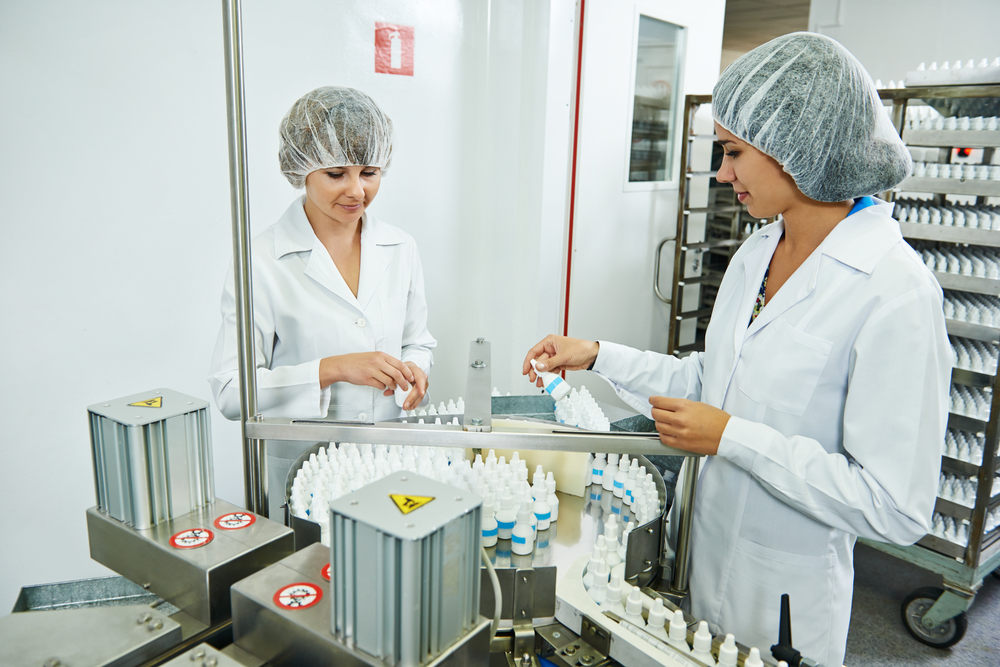
Conveyor Machine for small pharmaceutical bottles (Concept Image)
Quality control is enhanced with less likelihood of mistakes being made in the filling, counting, labelling and packaging pharmaceutical items. The production of small batches and switching between product lines is made simpler and faster using automated robotic technology.
With pharmaceutical companies always on the watch for improvements to cut production costs, improve turnover margins, increase value and make market access for treatments simpler, automation has held out the pledge of making this a certainty.
The changes and benefits robots could provide the pharmaceutical industry are seemingly limitless. From creating vast savings to increasing productivity and safety, it is the robots speed, accuracy, dependability and flexibility that make them such appreciated and valued investments.
The pharmaceutical industry is looking to enhance the sustainability of its operations. To do this, drug manufacturers have had to reduce waste and impurities, and not to mention, save energy. The amplified efficiency and dependability that robots deliver also signifies that there are far fewer discarded products and wasted materials. Robots in the lab, life science and pharmaceutical applications accomplish tasks at rates outside human capability. These robots function in potentially precarious settings in proximity to biological hazards, the danger of radioactive contamination, and toxic chemotherapy compounds. Many companies within the industry see the benefits of the automated process.
As the demands for new drugs and medicine grow, the pharmaceutical industry is continuously looking for new ways to increase productivity. Robotic technology can be an excellent investment. The benefits and the return of such an investment will repeatedly come in the form of energy savings, flexibility, high-speed production and increased quality.